NEWS&EVENT
Quality is our core our concept
Rubber formula design: the effects of white carbon black, stearic acid, zinc oxide, and sulfur
Release time:
2025-05-12 14:01
Source:
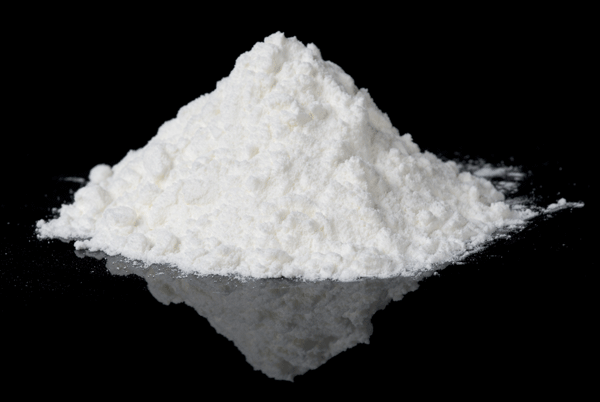
The rubber formula system mainly consists of three major systems: 1. Basic composition system: raw rubber matrix, reinforcement filling system, and vulcanization crosslinking system; 2、 Collaborative reaction system: activation system, coupling agent system; 3、 Functional regulation system: protective system, processing aids.
The following is a rubber basic formula design guide that includes white carbon black, stearic acid, zinc oxide, and sulfur, combined with functional synergy and process points:
1、 Basic formula composition and typical dosage (phr)
component | Universal formula | High reinforcement formula | Transparent product formula |
---|---|---|---|
rubber | 100 | 100 | 100 |
White carbon black | 30~40 | 50~60 | 20~30(high-purity) |
stearic acid | 1.5~2.5 | 1.0~2.0 | 0.5~1.0 |
zinc oxide | 3.0~5.0 | 3.0~4.0 | 1.5~2.5(reactivity) |
Sulfur | 1.5~2.5 | 1.0~1.5 | 0.5~1.0 |
accelerator | 1.0~2.0 | 1.5~2.5 | 1.0~1.5(No nitrosamine) |
coupling agent | 2.0~4.0 | 3.0~5.0 | 1.0~2.0 |
antioxidant | 1.0~2.0 | 1.5~2.5 | 1.0~1.5(anti-yellowing) |
2、 The core components and synergistic mechanism of white carbon black provide physical reinforcement (tensile strength+30-50%), adjust hardness (50-70 Shore A), and reduce rolling resistance (tire application). Collaboration: It needs to react with coupling agents (such as Si69) to improve the interface bonding with rubber; Stearic acid can enhance its dispersibility in non-polar rubber. 2. The combination of stearic acid and zinc oxide produces zinc stearate, which accelerates sulfurization (shortens T90 time by 20-30%), neutralizes acidic substances, and improves processing fluidity. Collaboration: Zinc oxide, as an alkaline substance, neutralizes the hydroxyl groups on the surface of white carbon black, reducing the structuring of the rubber material. Sulfur+accelerator function: Sulfur forms a cross-linked network (mainly composed of polysulfide bonds), and accelerators (such as TBBS) regulate the vulcanization rate and cross-linking density. Collaboration: Zinc oxide accelerates the decomposition of accelerators, while stearic acid adjusts the polarity of the rubber material to facilitate sulfur dispersion.
3、 Key control of mixing sequence in processing technology Stage 1: Raw rubber → White carbon black+Coupling agent (high-speed dispersion for 10-15 minutes, temperature ≤ 120 ℃). Stage 2: stearic acid → zinc oxide → anti-aging agent (mixed at medium speed for 5 minutes) Stage 3: sulfur+accelerator (mixed at low speed for 3 minutes, final temperature ≤ 100 ℃). Sulfurization condition temperature: 150-170 ℃ (adjusted according to the type of accelerator, such as the post effect accelerator can be increased to 175 ℃). Time: T90+10% (ensure complete cross-linking and avoid returning to the original state)
4、 Common Problems and Solutions
problem | reason | countermeasure |
---|---|---|
Poor dispersion | White carbon black aggregation and insufficient coupling agent | Raise the mixing temperature to 130 ℃ and add dispersants (such as PEG4000) |
Slow vulcanization speed | Low dosage of accelerator and poor activity of zinc oxide | Switching to overspeed accelerators (such as DTIM) and using nano zinc oxide |
The product is brittle | Excessive cross-linking density and excess white carbon black | Reduce sulfur to 1.0 phr and add plasticizers (such as cyclohexane oil) |
White carbon black