NEWS&EVENT
Quality is our core our concept
Application of Precipitation Method White Carbon Black in Rubber Foam Materials
Release time:
2025-06-09 08:41
Source:
As an important inorganic filler, precipitated white carbon black has unique application value in rubber foam materials. Its structural characteristics (such as high specific surface area and surface hydroxyl distribution) and physicochemical properties make it play a key role in improving the mechanical properties, cell structure, and functionality of foam materials. The following analysis focuses on application principles, performance impact/practical application points, and optimal addition amount, hoping to inspire and help you:
Ⅰ、 The characteristics of precipitated white carbon black and its compatibility with rubber foam materials
1. Structure and physicochemical properties
Precipitation method white carbon black is prepared by reacting soluble silicates (such as sodium silicate) with acid for precipitation, and has the following properties:
① High specific surface area (50~300 m ²/g): Provides abundant interface interaction sites, forming physical adsorption or chemical bonding with rubber molecular chains (after hydrogen bonding, silane coupling agent modification);
② Surface hydroxyl groups (Si OH): Strong hydrophilicity, prone to aggregation without treatment, but can be modified into hydrophobicity through silane coupling agents (such as Si-69, Si-75) to improve compatibility with rubber;
③ Controllable particle size (micrometer to nanometer): The smaller the particle size, the more significant the reinforcement effect, but the difficulty of dispersion increases.
2. The demand for rubber foam materials
Rubber foam materials (such as EPDM, NR, SBR, CR, etc.) must meet the following requirements:
① Lightweight (density 0.1~0.8 g/cm ³);
② Uniform pore structure (with fine pores and high closure rate to enhance thermal insulation, sound insulation, and shock absorption performance);
③ Mechanical strength (tensile strength, tear strength, compressive permanent deformation, etc.);
④ Weather resistance and functionality (resistance to aging, high and low temperatures, chemical media, etc.). Precipitation method white carbon black can meet the above requirements through mechanisms such as filler reinforcement and bubble stabilization.
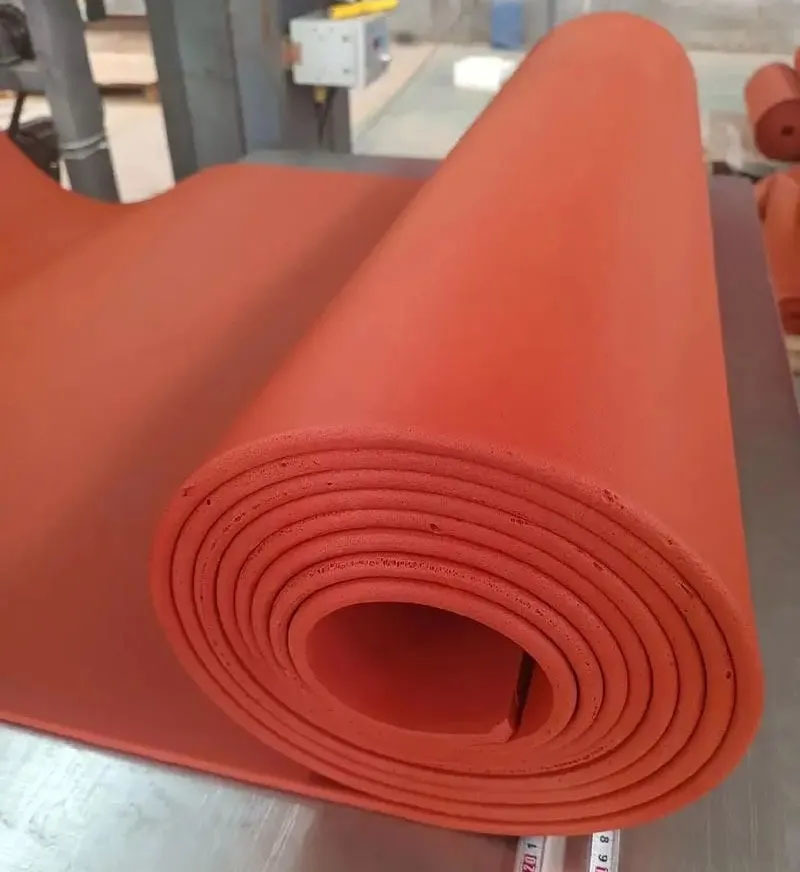
Ⅱ、 The core role in rubber foam materials
1. Mechanical performance reinforcement: improving the strength and toughness of foam materials
Filler reinforcement mechanism: The high specific surface area of white carbon black forms a "physical cross-linking network" with rubber molecular chains, limiting molecular chain slip and thereby improving:
① Tensile strength: For example, adding 30 parts (phr) of modified white carbon black to EPDM foam material can increase tensile strength by 20% to 30%;
② Tear strength and wear resistance: Especially under dynamic loads (such as shock absorbers), the rigid particles of white carbon black can disperse stress concentration points and reduce crack propagation;
③ Compression permanent deformation: improves the resilience of foam materials, suitable for scenarios such as seals that require long-term elastic retention.
Comparison with carbon black: White carbon black has no coloring properties in light or colored foam materials, and its weather resistance is better than carbon black, making it more suitable for outdoor applications (such as building sealing strips).
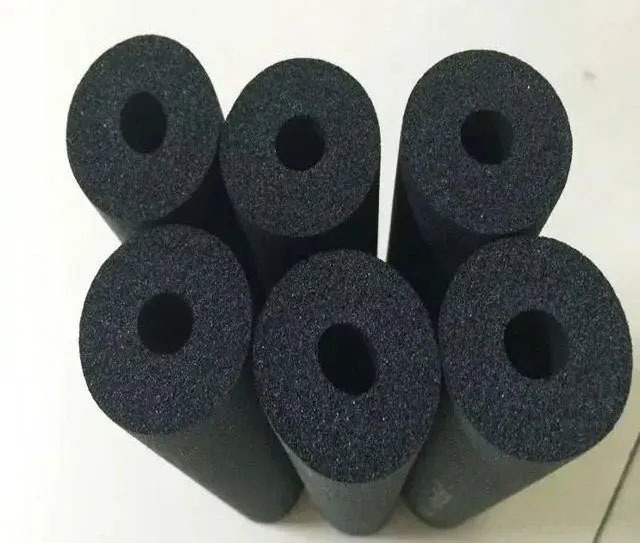
2. Regulating the pore structure: promoting uniform foaming and bubble stability
① Bubble nucleation and stabilization:
⑴ White carbon black particles can serve as nucleation sites for bubbles, reducing the surface energy required for bubble formation, promoting uniform nucleation, and reducing the generation of large pores;
⑵ Its surface hydroxyl groups or modified hydrophobic groups can adsorb at the gas-liquid interface, forming a "particle stable layer" that inhibits bubble coalescence or rupture, and improves cell uniformity (reducing cell diameter and increasing closed cell rate).
② Foaming ratio and density control: By adjusting the amount of white carbon black (usually 5-50 phr), the foaming density can be controlled within a certain range:
When the dosage is low (<10 phr), it mainly plays a nucleating role, increases the foaming ratio, and reduces the density;
When the dosage is high (>20 phr), the viscosity of the system increases, the resistance to bubble expansion increases, the density increases, but the pores become finer.
3. Enhance functionality: heat resistance, weather resistance, and insulation
① Heat resistance: The inert structure of silica can improve the thermal stability of foam materials and delay rubber degradation at high temperatures. For example, after aging at 150 ℃, the tensile strength retention rate of EPDM foam materials containing white carbon black is 15% to 20% higher than that of the untreated system;
② Weather resistance: White carbon black does not react with ultraviolet rays, ozone, etc., which can reduce the oxidative degradation of rubber matrix. It is suitable for outdoor waterproofing membranes, automotive sealing strips, etc;
③ Insulation: White carbon black itself is an insulator, and its addition can enhance the dielectric properties of foam materials, which are used as shock absorbers and insulation components for electronic devices.
4. Improve processing technology performance
① Adjusting the viscosity of the mixed rubber: White carbon black can increase the viscosity of the rubber material, improve the "gas retention" during the foaming process, and prevent the collapse of the foam caused by gas escape;
② Synergistic effect with foaming agent: The weakly acidic groups on the surface of some white carbon black can adjust the decomposition temperature and rate of foaming agents (such as AC foaming agents), promote the synchronization of foaming and vulcanization, and improve process stability.
Ⅲ、 Key application technologies and precautions
1. Surface modification: improving compatibility with rubber
① The problem with unmodified white carbon black: The surface hydroxyl groups are prone to form hydrogen bonds with polar groups in rubber (such as a small amount of polar groups in NR), but the overall hydrophilicity is strong, and its compatibility with non-polar rubber (such as EPDM, SBR) is poor, leading to aggregation and uneven dispersion, resulting in a significant increase in rubber viscosity.
● Modification method:
⑴ Silane coupling agent treatment: such as using mercapto silane (Si-69) and vinyl silane (A-171), hydrophobic groups are grafted onto the surface of white carbon black through hydroxyl condensation reaction, reducing surface energy, improving dispersibility, and forming a "white carbon black silane rubber" chemical link to enhance interfacial bonding;
⑵ Organic coating: Physical coating with stearic acid, silicone oil, etc. to reduce agglomeration tendency, suitable for low filling systems with low strength requirements.
2. Usage optimization: Balancing strength and lightweight
① Low filling (5-15 phr): mainly aimed at improving the cell structure, with high foaming ratio and low density, suitable for thermal and sound insulation materials;
② Medium filling (20-30 phr): Balancing strength and lightweight, suitable for shock absorbers and seals;
③ High filling (>40 phr): The strength is significantly improved, but the foaming ratio decreases and the density increases. It is necessary to use efficient dispersion processes (such as twin-screw mixing) to avoid processing difficulties.
3. Compound with other fillers
① Compound with calcium carbonate: Calcium carbonate has low cost and high density. When combined with white carbon black, it can reduce costs while offsetting the weakening of strength caused by calcium carbonate through the reinforcing effect of white carbon black. It is suitable for cost sensitive building foam materials;
② Compound with carbon black: In dark systems, a small amount of carbon black (5-10 phr) can be combined with white carbon black to enhance conductivity (anti-static requirements), while using white carbon black to improve cell uniformity.
4. Process matching: control of mixing and foaming conditions
① Mixing process: White carbon black has a high oil absorption value, and needs to be added step by step during mixing to avoid excessive thickening of the rubber material; Modified white carbon black can be more quickly compatible with rubber and shorten mixing time;
② Foaming temperature and time: White carbon black (especially unmodified) may slightly delay the decomposition of foaming agents. It is necessary to optimize the foaming temperature (usually 160-200 ℃) through DSC and other methods to ensure that vulcanization and foaming are completed synchronously, avoiding "sulfur deficiency" or "cell collapse".
Ⅳ、 Typical application scenarios
1. Construction field
① Waterproof sealing material: EPDM/white carbon black foam sealing strip, with high elasticity, weather resistance and aging resistance, used for door, window and curtain wall joints;
② Thermal insulation board: NR/white carbon black foam material, which reduces thermal conductivity through a fine closed cell structure, suitable for wall insulation.
2. Automotive industry
① Shock absorber: SBR/white carbon black foam buffer block, absorbs vibration and maintains high resilience, used for suspension systems;
② Engine compartment seal: CR/white carbon black foam material, oil and heat resistant, suitable for high temperature environment of the engine.
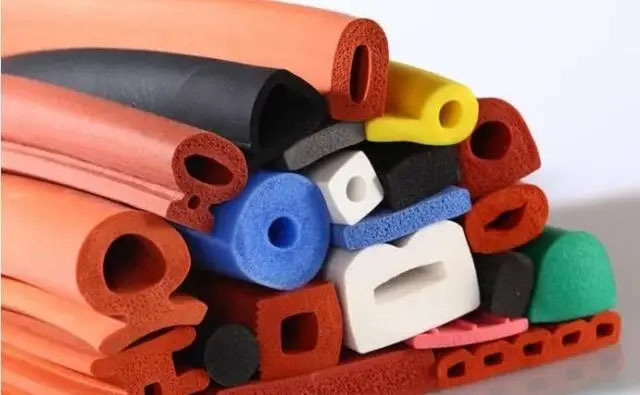
3. Electronics and Packaging
① Electronic device cushion: EPDM/white carbon black foam material, lightweight, insulating and shock-absorbing, protecting precision components;
② Food packaging sealing layer: White carbon black filled NR foam material that meets food contact standards, has good sealing performance and is safe and non-toxic.
4. Sports and daily necessities
① Sports sole foam material: SBR/white carbon black system, enhances the wear resistance and elasticity of the sole, while achieving lightweight through cell regulation;
② Fitness mat: EPDM/white carbon black foam material, non slip, shock-absorbing, and aging resistant.
Ⅴ、 Development Trends and Challenges
1. Greening: Developing halogen-free and low VOC white carbon black filling systems to meet environmental requirements;
2. Functional integration: By grafting functional groups (such as antibacterial and thermal conductive groups) onto the surface of white carbon black, foam materials are endowed with more functions;
3. Nanocomposite technology: interface control between nanoscale precipitated white carbon black and rubber, further enhancing strength and foam stability
4. Cost control: Optimize the production process of white carbon black, reduce modification costs, and promote its application in mid to low end foam materials.
Ⅵ、 Analysis of the optimal addition amount of precipitated white carbon black in rubber foam materials
1. Key factors affecting the addition amount of precipitated white carbon black
① Rubber substrate type
⑴ Polar rubber (such as NBR, CR): It has good compatibility with white carbon black and can be added in an appropriate amount, usually 15-30 parts (based on 100 parts of the rubber matrix, the same below). For example, in NBR foam seals, adding 20-25 parts of precipitated white carbon black can balance strength and elasticity.
⑵ Non polar rubber (such as EPDM, NR, SBR): relies on silane coupling agents to improve compatibility, with a general addition amount of 10-20 parts. In EPDM foam board, 15 parts of white carbon black combined with 1-2 parts of silane coupling agent can balance foam uniformity and mechanical properties.
② Foaming process and foaming agent types
⑴ Chemical foaming (such as AC foaming agent): The rubber material needs to maintain an appropriate viscosity at the decomposition temperature of the foaming agent. Excessive addition of white carbon black can cause a sharp increase in viscosity and hinder gas diffusion. It is recommended to add 10-20 parts;
⑵ Physical foaming (such as nitrogen and carbon dioxide): has low sensitivity to the viscosity of the rubber material, and can be appropriately increased to 20-25 parts of white carbon black to enhance the strength of the foam wall and reduce pore breakage.
③ Balancing performance requirements
⑴ High strength requirements: For example, wear-resistant foam soles can increase the amount of white carbon black to 25-30 parts, but need to be combined with plasticizers (such as phthalates) to improve processing flowability;
⑵ High elasticity/low density requirements: For cushioning foam materials, the addition amount should be controlled at 5-15 parts to avoid the influence of the rubber material being too hard on the foaming ratio.
④ Surface treatment and additive combination
(1) The amount of untreated precipitated white carbon black should be controlled at 10-15 parts, otherwise it may lead to the structuring of the rubber material (abnormal increase in viscosity);
After treatment with silane coupling agent, the addition amount can be increased to 20-30 parts, and the dispersibility is better. For example, 15 parts of treated white carbon black combined with 1.5 parts of Si-69 can increase the tensile strength by more than 30% in EPDM foaming.
Recommended addition amount for typical application scenarios
Rubber matrix | Application scenarios | Addition amount of precipitated white carbon black (parts) | Key additives |
EPDM | Waterproof membrane, shock-absorbing pad | 10-20 | Silane coupling agent (1-2 parts), zinc oxide |
NR/SBR | Foam sole, tire liner | 15-25 | Sulfur, accelerator, plasticizer |
NBR | Oil resistant foam seal | 20-30 | Carbon black (used in combination), magnesium oxide |
CR | Weather resistant foam profiles | 15-25 | Accelerator, anti-aging agent |
⑤ Experimental principles for determining the optimal addition amount
⑴ Single factor variable method: fix other formulations (such as rubber, foaming agent, vulcanization system), adjust the amount of white carbon black in a gradient of 5 parts (such as 10, 15, 20, 25 parts), test: Mooney viscosity of the rubber material (affecting processability) → density, cell size and uniformity after foaming → mechanical properties (tensile strength, elongation at break, compression permanent deformation).
⑵ Performance balance point: The optimal addition amount usually occurs in the range where the improvement in mechanical properties tends to be flat and the foaming ratio does not significantly decrease. For example, in a certain EPDM formula, when the amount of white carbon black increases from 10 parts to 15 parts, the strength increases by 20% and the foaming ratio decreases by 5%; Continuing to increase to 20 parts, the strength increases by 5%, and the foaming ratio decreases by 15%, then 15 parts is the better solution.
⑶ Cost and process adaptability: White carbon black is more expensive than carbon black, and excessive addition will increase costs; At the same time, the load of the mixing equipment needs to be considered (high addition may lead to high mixing temperature, affecting the stability of the additives).
⑥ Precautions
⑴ Dispersion priority: Regardless of the amount added, the uniform dispersion of white carbon black is crucial. It is recommended to use a two-stage mixing process (mixing white carbon black with coupling agent first, and then adding other additives);
⑵ Humidity control: Precipitation method white carbon black has strong hygroscopicity and needs to be dried (100-120 ℃, 2 hours) before use to avoid affecting the decomposition of foaming agents or the burning time of rubber materials;
⑶ Collaborative reinforcement system: It can be used in combination with fillers such as carbon black and nano calcium carbonate. For example, "10 parts white carbon black+5 parts carbon black" can balance strength and cost in NR foaming.
The optimal addition amount of precipitated white carbon black in rubber foam materials is usually 10-30 parts, which needs to be optimized through experiments according to the rubber type, foaming process, and performance goals. If using non-polar rubber such as EPDM and NR as examples, the recommended addition amount of silica treated with silane is 15-20 parts; Polar rubber (such as NBR, CR) can be appropriately increased to 20-30 parts. In the experiment, special attention should be paid to the balance of viscosity, foaming uniformity, and mechanical properties of the rubber material. If necessary, the comprehensive effect can be optimized by compounding additives.
summarize
Precipitation method white carbon black has become an indispensable functional filler in rubber foam materials through its unique reinforcement mechanism and bubble regulation ability. The core of its application lies in balancing the strength, lightweight, and functionality of materials through surface modification, dosage optimization, and process matching. In the future, with the increasing demand for greenization and functionalization, the application of precipitated white carbon black in rubber foam materials will expand to higher performance and wider scenarios.
white carbon black,precipitated silica,silica application,additives